In today's fast-paced manufacturing landscape, the demand for efficiency and speed has never been greater. As businesses strive to bring products to market quicker than ever, one technology stands out as a key player in this race: rapid injection molding. This innovative approach to injection molding not only enhances production speed but also allows for greater flexibility and precision in the design process. Understanding rapid injection molding is essential for companies looking to stay competitive and meet the evolving needs of consumers.
As we delve into the intricacies of rapid injection molding , we will explore its benefits, applications, and the technologies driving its growth. From prototype development to low-volume production runs, this method is transforming how manufacturers think about production and design. Join us as we unlock the potential of rapid injection molding and discover how it can reshape the future of manufacturing efficiency.
Technological Innovations in Rapid Injection Molding
The landscape of rapid injection molding is experiencing a significant transformation thanks to advancements in technology. One of the key innovations is the development of high-speed injection machines. These machines are designed to operate at faster cycle times, allowing for more efficient production. The increased speed not only boosts productivity but also minimizes the time products spend in the production line, thereby reducing lead times and meeting the increasing market demand for quick turnaround.
Another noteworthy advancement is the integration of computer-aided design (CAD) and computer-aided manufacturing (CAM) technologies. These tools enable engineers and designers to create highly intricate molds with greater precision and speed. The ability to simulate the injection molding process virtually also aids in identifying potential issues and optimizing the design before actual production begins. As a result, there is a notable decrease in material waste and an overall enhancement in the quality of the final products.
Moreover, the emergence of advanced materials is reshaping rapid injection molding capabilities. New high-performance polymers and composites are being developed, allowing for better durability and functionality of molded parts. These materials not only cater to specific industry requirements but also allow for lighter and more sustainable products. The combination of these innovations is driving the future of rapid injection molding towards a more efficient and environmentally friendly paradigm, ultimately benefiting manufacturers and consumers alike.
Benefits of Rapid Injection Molding
Rapid injection molding offers significant advantages that set it apart from traditional molding techniques. One of the most notable benefits is the reduction in lead time for producing parts. With the ability to quickly create prototypes and transition to production, companies can accelerate their product development cycle, bringing innovations to market faster. This speed is essential in today's competitive landscape, where being first can lead to substantial market advantages.
Another key benefit is cost-effectiveness, especially for shorter production runs. Rapid injection molding utilizes quick-turn mold fabrication techniques, which require less time and resources compared to conventional methods. This allows companies to produce smaller quantities without incurring the high costs associated with traditional molds, making it an attractive option for startups and businesses testing new product concepts. As a result, companies can invest more in design and development while keeping manufacturing costs manageable.
Lastly, rapid injection molding enhances design flexibility, enabling manufacturers to experiment with complex geometries and materials. This adaptability allows designers to refine their creations iteratively, leading to improved functionality and aesthetics in the final products. Additionally, with advancements in materials science, rapid injection molding can accommodate a wider range of materials, further expanding design possibilities and applications across various industries.
Future Trends and Predictions for Efficiency
As the demand for rapid injection molding continues to grow, advancements in technology are expected to enhance efficiency significantly. One promising trend is the integration of artificial intelligence and machine learning into the design and manufacturing processes. These technologies can analyze vast amounts of data to optimize mold design, predict potential issues, and streamline production schedules, resulting in shorter lead times and reduced wastage. This not only speeds up the manufacturing process but also ensures consistent quality in the final products.
Another key trend is the increasing use of sustainable materials and processes. The industry is gradually shifting towards bio-based polymers and recycled materials, which can provide the same performance characteristics while being more environmentally friendly. As manufacturers adopt these materials, rapid injection molding can evolve to minimize its carbon footprint. Innovations in energy-efficient machinery and automation are also expected to play a vital role in increasing the sustainability of the process, making it more attractive for companies focused on reducing their environmental impact.
Finally, the progression of digital technologies, such as 3D printing, is likely to merge with rapid injection molding practices. This hybrid approach can allow for quicker prototyping and the production of complex geometries that were previously difficult to achieve with traditional methods. By combining the strengths of both technologies, manufacturers can increase flexibility, reduce costs, and enhance the overall efficiency of the production process. As these trends take shape, the future of rapid injection molding looks promising, offering new possibilities for manufacturers and consumers alike.
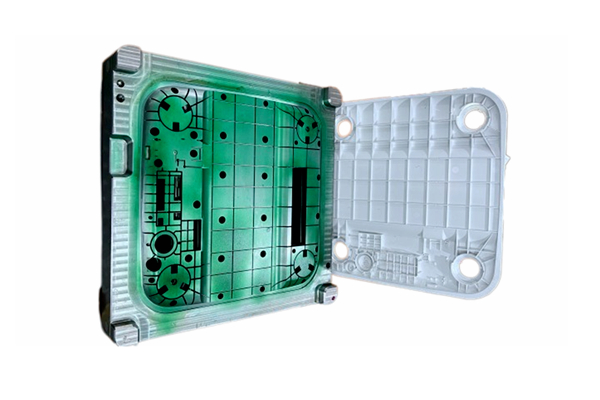